16.1 总 则
1) 本工艺适用于汽机范围内管道、容器、承重构架及结构部件的焊接及热处理工作。
2) 本工艺适用于低碳钢,普通低合金钢,耐热钢、不锈钢、铜及铜合金、铝及铝合金、铸铁等材料的手工电弧焊,手工钨氩弧焊和O2 C 2H2气焊。
3) 有关安全方面,应遵守安全防火等规程的有关规定。
4) 焊缝检查和焊工考核及质量验收应遵照有关射线超声检验等规定及焊工考试的规则执行。
5) 对焊工及热处理工的要求,见电力建设施工及验收技术规范(火力发电厂焊接篇)。
16.2 焊接工艺
16.2.1焊接材料
16.2.1.1焊条、电丝的选择,具体按工程一览表选择
1) 对同种类钢,机械性能及化学性能,化学成分与母材相近,焊条的合金元素的含量应略高于母材,Ar弧焊焊则要求与母材相同,化学类有钢要求抗蚀性同母材相同。
2) 对焊接质量要求高,裂纹倾向大的材料和结构,应选用低氢型焊条。
3) 对于异种钢,两非“A”体钢同类组织异种钢应选择靠近低合金侧或选其中间合金含量的焊条和焊丝;两非“A”体一同组织异种钢应选择能获得综合性能好的组织的焊条,焊丝,两材料其中之一为“A”体不锈钢时应选用高Ni不透钢焊条,对各异种钢结构,可参考附表16-1选择。
4) 对低碳钢,普通碳素结构钢,选用相应强度等级的结构焊丝,焊条。
5) 焊条的直径选择,必须是在保证操作工艺性良好,成型美观,保证焊接质量的前提下尽可能选择较大直径的焊条,对于承压管道的多层焊,底层采用?2.5mm焊条,第2-3层选用?3.2mm焊条,以后各层选用?4.0mm焊条,对应力大,裂纹倾向大的高合金钢,高碳钢,应选用较小的焊条直径。
16.2.1.2钨极的选择:目前市场上有纯钨极,钍钨极和铈钨极三种,纯钨极及钍钨极已趋于淘汰不再被采用。最好选用铈钨极。其直径据所用的电流进行选择,各种规格的钨极所适应的电流范围如表16.1.
表16.1 钨 极 许 用 电 流 表
钨极直径mm 焊接电流A
正极性 反极性
0.5 20 ---
1.0 80 ---
1.6 150 20
2.4 250 30
3.2 400 40
4.0 500 55
4.8 800 80
6.4 1100 125
16.2.1.3对焊接材料的要求
1) 焊丝、焊条应保持清洁,无锈、无油污。应有生产厂的出厂产品合格证及技术说明书。其质量应符合国家标准。
2) 有良好的工艺性能。应引弧容易,燃烧稳定,飞溅小。其使用性能和工艺性能应符合工程的需要。
3) 焊丝、焊条在使用前及使用中应保持干燥,药皮不能出现变质的现象。
4) 氩气的纯度应大于99.5%
16.2.2焊接电源种类及极性的选择
1) 碱性低氢型焊条,除铝及其合金以外的常用材料的钨氩弧焊(TiG),必须采用直流焊接电源。碱性低H型焊条采用反极连接。钨极氩弧焊采用正极性连接。
2) 非重要部件采有和酸性焊条焊接时,可选用交流弧焊电源。
3) 铝及铝合金的TiG焊,采用专用的交流TiG焊机。
4) 焊接电源的额定容易满足焊接要求,交流弧焊的空载电压为55~75V,直流弧焊电源的空载电压为60~90V,但不能过高,交流弧焊电源U0≤80V,直流弧焊电源U0≤90V(整流器)和U0≤100V(弧焊发电机)。要有较好的动特性和良好的徒降特性(对于手式焊),以便有良好的引弧和稳弧性能。几种弧焊电源的技术参数见附表16-2.外特性见附图16-1.
16.2.3焊前准备
16.2.3.1焊缝位置的确定。焊缝应避开力集中区,便于施焊及热处理工作的进行,具体有以下要求:
1) 管道对接焊缝中心线距管子弯曲起点应不小于管了的外径,并且不小于100mm(成品弯头除外),与支架边缘距离不小于50 mm,对于需要预热及焊后处理的管件,焊缝中心线与弯曲起点及支架的距离应满足热处理时保温层及炉具设置的要求,应大于保温层宽度的三分之二。
2) 管接头和仪表插座应尽可能避开管道上的焊缝及热影响区。
3) 筒体的对焊接焊口,其中心线距离封头弯曲起点应不小于壁厚加15mm。
4) 纵向焊缝的筒体和封头,其两纵向焊缝距离应大于三倍壁厚,且>10mm。
5) 焊接管的管孔要避开焊缝及热影响区,否则必须:
(1) 管孔两侧60mm(若d>60mm则取d值),的范围的焊缝要经射线探伤检查合格。
(2) 孔边缘不在焊缝缺陷上。
(3) 接头需经焊后去应力处理。
6) 搭接焊缝的搭接长度大于五倍母材厚度,并且>30mm.
16.2.3.2坡口选用,要本着保证焊接质量高,金属充填量少,便于操作,改善劳动条件,减少焊接应力与变形,利于质量检查等原则进行,对于厚度δ<3mm的一般非重要结构及管子无需要坡口。对于δ<16mm的板,管结构,采用“∨”型坡口。对于δ<16mm限于单面焊的板,管结构采用双“∨”型坡口,对于δ<16mm可双面施焊的板管结构采用“x”坡口,对于要求焊件的变形及应力极小,且只允许单面施焊的板,管结构采用“∨”,“∨/U”坡口。各种坡口及尺寸见附图12-2,根部采用氩弧焊时钝边厚度可大于手工电弧焊时钝边厚度。
16.3.2.3母材下料与对口。
1) 焊件下料以机械方法为宜,淬硬倾向较大的合金钢用热加工方法下料时,切口部位必须进行退火处理,或用机械方法除去热影响区,一般非淬硬性材料的气割坡口,应除去表面氧化皮和污物并修整平齐,高合金钢不得进行气割加工坡口。
2) 剪床切割的钢材边缘不应有裂纹,毛刺和缺棱等缺陷。
16.2.3.4对接焊口的端面斜度<1%d≯2mm,(d-管外径)
16.2.3.5坡口以外两侧10-15mm范围内,焊前进行清理油、锈、污物,并检查应无裂纹,夹层等缺陷。
16.2.3.6焊件组装时应垫置牢固,以免在焊接和热处理过程中变形。
16.2.3.7对口要求内外壁平齐,对于内径不等的板件和管件,应按附图16-4进行加工处理,对接单面焊的局部错口值不应超过壁厚的10%,且<1mm。对口间隙应符合表16.2的要求。焊口处母材应无缺陷。
表16.2 坡 口 间 隙 尺 寸 表 单位:mm
接 头
型 式 坡 口
形 式 焊 接
方 法 坡 口
间 隙 接 头
型 式 坡 口
形 式 焊 接
方 法 坡 口
间 隙
D S、 Q 1-2 D X S 2-3
V 1-3
A 2-2.5
T 无坡口 S 0-2
U.V/U A 1.5-2 V A 2-2.5
S 2.5-3 S 2-3
双V A 2.0-3.5 K S 1-2
S 2.5-5 搭 接 S 0-1
A 2.0-3.5
S 2-4
16.2.3.8除原设计冷拉口外,禁止强力对口。
16.2.3.9严禁在坡口间隙内填塞它物。
16.2.3.10焊接场所应高防风、雨、雪设施及防寒设施。
16.2.3.11焊条使用前应进行烘干,各类焊条的烘干温度与时间见表16.3
表16.3 各 类 焊 条 的 烘 干 温 度 与 时 间
焊 条 类 别 烘干温度(℃) 烘干时间
(小时) 准 注
国外碱性焊条 250 3 现场剩余焊条次日使用前烘干
100℃,1小时
国内酸性焊条 150 1-2
国内碱性焊条 350 1-2
16.2.3.12焊丝使用前应进行除污除锈,直到呈现金属光泽为止。
16.2.4焊前预热及补偿加热
16.2.4.1焊接时允许的最低环境温度。
1) 低碳钢为-20℃。
2) 低合金钢及变通低合金钢-10℃。
3) 中、高合金钢,中、高碳素钢为0℃。
16.2.4.2预热温度的选择,常温下各种钢件的预热温度按工程一览表选择或按工艺曲线选择
1) δ<6mm的合金板件及管件在负温时预热温度应比常温时预热温度值高20-50℃。
2) δ<6mm,的合金钢板及管件和δ<15mm,的低碳钢,在环境为负温时亦应预热100-150℃。
3) 异种钢焊接,预热温度应按可焊性差的一侧选择。
16.2.4.3接管座与主管焊接时,按主管规定选择。
16.2.4.4非承压部件与承压部件焊接时,按承压部件的规定选择。
16.2.4.5加热热源的选择。
1) 对于预热要求不严格的非承重,承压部件及变形度要求不严格的工件,或选用火焰加热。
2) 对预热均匀程度要求较严格的结构简单的薄壁承压部件,应用电阻炉及履带加热器加热。
3) 对预热均匀程度要求严格,结构复杂和厚壁(δ<25mm)部件采用电感应加热。
16.2.4.6预热段宽度,自焊缝中心线开始每侧不小于3δ,且≮50mm。
16.2.4.7保温层,保温材料选用硅酸铝纤维。
1) 保温层宽度,采用履带加热器加热时,其宽度应比加热器每侧增宽30mm,采用电感应加热器。其宽度应比加热线圈边缘每侧增宽30mm。
2) 保温层厚度,采用履带加热器及电阻炉时,厚度选为30-50 mm;采用电感应加热时厚度选为20-30mm。
16.2.5焊接
16.2.5.1点固焊:对口要求的各项条件达到后,进行点固焊,点固焊的焊接工艺参数,焊接材料,焊工等条件与正式底层焊缝施工相同,点固焊缝的分布应在整个焊缝上均匀分布,d<?100- ?200mm,的管子采用三点,d> ?200mm的管子采用四点点固。焊缝厚度应与底层焊缝相同,焊缝长度在10-30 mm之间选择,管径大时选择较大的焊缝长度。
16.2.5.2底层焊缝的焊接;对于要求单面焊双面成型的底层焊缝有氩弧焊和电弧击穿焊两种方法;对于不要求透度的焊缝可不采用氩弧焊及击穿焊法而采用非击穿电弧焊。
1) 需要氩弧打底的结构:工作压力>64kg/cm2或T>450℃汽、水管道,再热管道,冷却水及润滑油,调速油管道,不锈钢管道,主汽,再热蒸汽主管道上的疏水管道,15M03C 以上合金成分的合金管道氩弧打底进行充氩保护。
2) 对于振动轻,压力小而对工质纯净度要求高或要求抗裂性好的板及管结构,有较大的空气流或负压并无法消除时,可采用击穿焊。
3) 对抗裂性要求小的变通结构,如承重,承压部件可采用非击穿法焊接。
4) 氩弧打底焊接工艺参数按氩弧焊工艺选择。
5) 采用击穿法焊接底层焊缝时,应采用抬、顶、灭方法运条操作为宜,以使焊缝的成型良好及保证焊缝质量。
6) 底层焊缝的厚度应以所用焊条,焊丝的直径大小为宜。
16.2.5.3充填层及表面层焊接,以手工电弧连续运弧焊接为宜。
1) δ>4mm的工件采用多层焊。
2) 坡口宽度大于四倍焊条直径时采用多道焊。
3) 每道焊道的宽度为3-4倍的焊条直径,平均每层焊层的厚度等于所用焊条的直径,最大值≯3d焊条。
4) 各层道间的焊渣应严格清理,避免缺陷产生,底层焊缝经检查合格后应及时进行充填焊。
5) 多层多道焊的焊接顺序应合理安排,如图16.1,尽可能减少焊接顺序不合理造成的焊接应力。
图16.1
6) 各层道焊接电流的选择,依据IH=(30—50)d选择,d为焊条直径,单位为mm,IH为焊接电流,单位为安培,以在正常焊接速度下能形成并保持良好的椭圆开熔池为宜,严禁采用过大的焊接电流焊接而产生焊缝过烧,劣化焊缝质量,IH不得低于20d,防止出现未熔合缺陷,保证焊缝成型和焊接质量。
7) 焊接操作中严格控制焊缝形状系数,保证B/H=1.5左右,否则焊缝质量差,成型不好。
8) 多层多道焊缝的接头应相互错开10—20mm,收弧时应填满熔池,接头应叠压5—10mm。
9) 禁止在工件上随意引弧及试验电流和焊接临时支撑物。
10) 易淬硬裂纹的高合金工件,焊接时应设置引弧板。
11) 焊接时工件应防止冷却速度过大,(铸铁的冷焊除外)。除做好焊前准备的有关事项外,管道焊接还应防止穿堂风。
12) 直径大于194mm的管件,采用二人对称焊接,焊接过程中应保持二人采用的焊接线能量及其它焊接参数的一致性。
13) 焊缝除工艺或检查要求分次施焊外,应连续一次完成,否则应做好防裂措施,再焊前对焊缝进行检查是否出现裂纹,如有裂纹应首先清除,然后再进行焊接。
14) 直径大于1000mm的管道或容器的对接焊缝应采用“×”型坡口,以面焊的焊接工艺
15) 焊接过程中,如发现焊接缺陷,应及时进行挖补,焊缝上同一缺陷位置的挖补次数不得大于两次,需要立即热处理的接头,应在热处理后进行反修,反修后再进行一次热处理。
16) 表层焊缝应过度园滑,不得出现咬边及熔坑。宽度,加强高度及不均匀程度不应超出质量标准的合格范围。
17) 焊缝焊后,焊工要首先进行自检,自检合格后,在焊缝近区打上焊工代号钢印。
18) 对易产生延迟裂纹的钢焊后应及时热处理,否则应进行250℃-350℃后热,缓冷,其加热宽度与热处理相同。
19) 冷拉口应在焊接热处理完毕后,方可拆除冷拉工具。
16.2.5.4手工钨极氩弧焊工艺。
有关焊接电源,部分焊接材料,坡口型式及尺寸等选择见十六章焊前准备部分。下面着重介绍其他参数的选择及工艺方法。
1) 焊接参数选择。
(1) 焊接电流根据工件和预热的情况而定,工件的厚度大,导热系数大,预热温度低时,应选用较大的焊接电流。否则,应选用较小的焊接电流。焊接电流过小时,易产生未焊透,气孔和夹渣。焊接电流过大时,出现内凹,咬边,焊瘤,气孔,裂纹等缺陷。一般以使焊缝在正常焊接速度下形成并保持椭圆形溶池为宜,可参照表16-2-4选择。
(2) 焊丝直径的选择,应据工件厚度及坡口钝边厚度和焊接电流、坡口间隙而定,工件厚度、钝边度厚大;焊接电流大;坡口间隙大,焊丝直径应选大些。否则,应小些。可参照表16.4选择碳素钢,普低钢,耐热钢铁焊接参数。
碳素钢、普低钢、耐热钢TiG手弧焊
表16.4 规范喷咀直径D=8mm
板及钝边厚度 电 流 焊丝直径 焊接速度 气体流量
(mm) 正极性(A) (mm) (mm/min) (L/min)
0.9 100 1.6 300-370 4-5
1.2 100-125 1`.6 300-450 4-5
1.5 100-140 1.6 300-450 4-5
2.3 140-170 2.4 300-450 4-5
3.2 150-200 3.2 250-300 4-5
当工件为不锈 钢时,可按表16.5的参数选择
表16.5 不透钢对接TiG手工规范
板、钝边厚(mm) 间 隙
(mmi) 电 流
正极性(A) 焊 速
(mm/min) 钨 极?
(mm) 焊丝直径
(mm) 气体流量
(L/min)
1 0 50-80 100-120 1.6 1 4-6
2.4 0~1 80-120 100-120 1.6 2 6-10
3.2 0~2 105-150 100-120 2.4 2-3.2 6-10
4 0~2 150-200 100-150 2.4 3.2-4 6-10
4 0 100-150
150-200 120-160
120-150 2.4 3.2-4 6-10
(3) 钨极直径应依据所需的焊接电流按表16.1选择。
(4) 喷嘴直径应采用的钨极直径按下式计算选择。D=2dw +4(mm)。
(5) 氩气流量依据喷嘴直径D按Q=(0.8-1.2)D选择,D值大时,选择较大的系数,Q的单位为L/min.也可参照表16.4,表16.5选择。
(6) 预热温度选择,可低于电弧焊所采用的预热温度100-200℃左右。对于可焊性不很坏的钢及结构采用氩弧打底焊时不进行预热,对于X20GrMoV121等可焊性很差的钢,要求按工艺图所给出的预热温度值进行预热,对于散热系数很大的有色金属铜,铝及其合金应预热到300-450℃
(7) 坡口间隙按表16.2选择,不锈钢按表16.5选择,铜 、铝及其合金在铝及铝合金氩弧焊部分中说明。
2) 工艺方法
(1) 采用接触引弧时,不应用划擦法,应将钨极向坡口处轻轻一点,不得用力过猛,最好采用高频引弧装置线弧。
(2) 运弧,就采用直线开运弧,否则,焊枪的横向摆动幅度亦小于5mm。
(3) 收弧,应将电弧引向坡口边缘停弧,最好采用电流不衰减装置对电流进行衰减,焊缝中心突然继弧,不得在应力集中处停弧。
(4) 焊接过程,焊丝熔化端的端头不得离开保护区。
(5) 坡品及焊丝的清理应比电弧焊的要求严格,不得有油,锈等污物残留。
(6) 焊缝的背面,对于氧化钢应充氩保护,背面充氩保护的气体流量,就装设不影响焊枪中气体流量的另一套供气装置。其流量以不影响成型为宜。
(7) 合金钢大径厚壁管(?>200mm,δ>20mm)或裂纹倾向大的径管(?>200mm)采用二人对称焊接。
(8) 冷拉口应在充填焊及热处理后,方可松开冷拉工具。
(9) 焊接速度应适中,可参照表16.4及表16.5选用和控制,以在焊接中能保持稳定的椭圆开熔池为宜。
(10) 焊枪的角度,应始终保持与熔池处切线呈后倾70-80°角度,并保持喷嘴轴线始终在管中平面内。
16.2.5.5手工堆焊工艺。
堆焊种类较多,在此只交待有关手工电弧堆焊工艺。
1) 据工件的材质性能及化学性能,选择适当的焊接材料,有时还要据工件的使用要求选择焊接材料,有关堆焊材料的性能,成分见附表16-5。
2) 焊接材料的化学成分与基体有很大的差异时,就采用中间过渡层焊接方式,过度层的层数一般为一层,厚度不大于4mm。
3) 焊前,应对工件的被堆焊面,进行清理铣除死角修整园滑,将其表面的残余油,锈污物清理干净,露出金属光泽。
4) 前次堆焊的焊层应车削清除干净。
5) 清理后对被焊工件表面进行缺陷检验,无缺陷时方可做下一步的准备工作。
6) 对塑性差的材料,过渡层焊接材料就用“A”体焊条或Ni基焊条,其他过渡层按成分过渡的原则选择。
7) 对于易变形或易裂的材料,应进行适当的预热,对于高碳钢及厚壁普通钢,应预热100-250℃,对于裂纹倾向大的高合金钢等应预热250-400℃,对于散热系数大的有色金属,应预热300-500℃(铸铁等材料的冷焊除外)。此外还应根据焊接材料所需的预热温度综合考虑选择。常用堆焊焊条的预热附表16-4。
8) 焊条的烘干,使用前应对焊条进行适当的烘干,碱性焊条应进行350℃,1-2小时的烘干,酸性焊条应进行150℃,1-2小时的烘干。
9) 焊接中应采用小线能量,窄道,直线运条施焊,焊条金属应短路过渡,Ih=10(3.5-4)dH,L<50mm
10) 堆焊,对同质,同成分的母子材和焊条,其堆焊层数无要求,对于焊条成份与母材差异很大的堆焊层,如在低碳,低合金钢基体上堆焊硬质合金,堆层一般不能小于3层。每层厚度应≤dH(dH为焊条直径)。否则,堆焊层表面有较多的母材溶入,合金成份下降,性能差。但层数也不能过多,否则,堆焊层过厚,使内应力增加,易产生裂纹,一般不超过五层。
11) 合理地安排焊接顺序及排列焊道,使焊道在焊件的堆焊部位均匀分布。
12) 对于体积较小的工件,其热容量较小,应防止其过烧,减小焊接电流,增加息弧时间。
13) 对于非堆焊部位,应加以防护,以防被电弧及飞溅熔滴打伤,使工件报废。
14) 堆焊应一次完成,以防过大的周期性热应力作用,损坏工件。
15) 除一般单个小孔外,均不应局部堆补。必须局部堆补时,应采取必要的防变形及降应力措施,如采用冷焊法,选用高塑性,低强度焊条,对焊缝进行锤击消应力,焊后对焊件进行整体热处理等。
16) 堆焊层如要进行加工的,还应满足加工方面的要求,如堆焊层厚度应有足够的加工余量,硬度很高的堆焊层,在加工前应进行退火软化处理,加工后再进行淬火或正火加回火处理。
17) 对于要求焊后热处理的材料,还应按规定进行热处理,几种焊接材料堆焊后热处理参数见附表16-4。
18) 硬度较高,裂纹倾向较大的材料应控制其冷却速度,使其在降温过程中缓冷,一般在保温条件下冷却,(此条中的材料包括焊接材料及母材)。
19) 有关有色金属暹焊按有色金属的焊接工艺执行。
16.3 裂纹缺陷的挖补工艺
16.3.1清理裂纹及坡口加工
1) 对于裂纹倾向大的薄壁脆性材料,在打磨及铣削之前,在裂纹的两端点外5-10mm外钻截止孔,其直径视裂纹的横向受力大小而定,受力较大时,其孔么应大些,受力较小时其孔么就小些,一般孔径在3-6mm之间,防止裂纹在处理中扩展。
2) 用砂轮或用钢铣对裂纹进行铣磨,直到彻底清除裂纹,而后将侧面的棱角和死角进行磨光,其铣磨后的凹槽应便于以后的坡口制做。
3) 裂纹清理后,应对该部位进行表面探伤检验,如有裂纹没有被清除,就继续铣磨,直到检查无裂纹存在为止。
4) 坡口制作,将经检查的凹槽进一步打磨加工,制作成“V”型或“U”型坡口,其型式视工件坡口,两尖端应磨成缓坡形与工件表面过渡园滑。
16.3.2焊接材料的选择,据材料的性能选择。
1) 对于无需进行热处理的材料或热处理条件能达到的条件下,选用与母材化学成份相同等强度焊条。
2) 对于无热处理条件的结构和材料,且材料和结构要求应力小,变形小时,选用同强度的铬镍“A”体钢焊条。
3) 选用抗裂性好,有良好韧性的低氢型焊条。
4) 尽可能选用较小的焊条直径。
16.3.3用于焊接的电源,应采用直流反极性连接。
16.3.4焊条要按着规定,进行充分的烘干处理,一般为250℃-1.5小时。
16.3.5焊接规范及方法的选择。
1) 预热,对可焊性较好的材料及冷焊时,工作无需预热,可在作好焊接准备的情况下直接进行施焊;对于可焊性差的材料和结构,应按规定进行预热。组织应力很大的材料,预热温度应高于Ms。
2) 对于可焊性差的材料;除了按规定预热外,应设法减小结构的拘束度。
3) 对于焊缝强度要求不太高或非承压易裂部件及结构,可采用冷焊的焊接工艺,焊接时采用小电流,窄道,短段焊接,如焊缝长度较长时还应采取倒退焊法,焊接过程中,焊缝上任意两点的温度差不能大于40-50℃,同时对焊缝进行锤击消除应力。
4) 对于焊缝强度要求高的或承受强载荷可焊性差的部件及结构,应采用热焊工艺,整个焊接过程焊缝温度应大于Ms,焊后还应进行高温回火或消氢处理,加热时应考虑工件的变形,采用较慢的热处理加热速度,焊接时应采用小的焊接电流。
5) 对于变形和应力要求极严的焊接结构及工件,应采用钨极氩弧焊焊接方法。采用握弧焊工艺。
6) 尽可能采用多层,多道焊,焊缝与母材之间过渡应园滑,不得有咬边和留有弧坑,有延迟裂纹倾向的钢要及时进行热处理。
16.3.6缺陷焊缝挖补后的热处理参数及要求与正常焊后热处理相同。
16.4 几种常用材料室温下焊接时存在的问题和采取的措施
16.4.1碳素钢
16.4.1.1低碳钢(C<0.25%),焊接性能良好,一般不采取特殊的工艺措施。
16.4.1.2中碳钢(C=0.25-0.60%),高碳钢(C>0.60%)
1) 存在的问题:碳含量高,淬硬倾向大,易产生裂纹和气孔。
2) 措施:
(1) 焊条:选用低氢型焊条,使用前进行烘干350℃-1-2H,使用中严防潮吸。
(2) 焊接电源:采用直流反极性连接。
(3) 操作:逆向,短段,多层焊法,焊道在整个焊缝上均匀分布,较大的结构和焊缝长度采用二人对称焊接。
(4) 焊接电流:比焊接低碳钢所用的电流小于10-15%,采用小的焊接线能量。
(5) 预热:对中碳钢,预热100-250℃.对高碳钢,预热200-450℃.在整个焊接过程中,应始终保持预热温度。
(6) 焊后缓冷:中碳钢的冷却速度应<200℃/H,高碳钢的冷却速度<100℃/H。
(7) 焊后热处理:根据工件的焊接结构和含碳量,用途等决定是否进行进行热处理,对要求较高的高碳钢,中碳钢均应进行去应力退火,对组织应力极大的高碳钢应进行高温回火处理,去应力退火温度为450-650℃,高温回火温度为650-680℃。
16.4.2普通低合金钢(Me<3%)
普低钢一般焊接性能良好,结构不合理,工艺不当会出现一些缺陷。
16.4.2.1存在的问题:
HAZ区有一定的淬硬倾向在承受较大的应力情况下,易出现冷裂和再热裂纹,随着Ceg的增加,淬硬、冷裂倾向增加,Ceg=C+1/6Mn=1/5(Gr+Mo+V)+1/15(Ni+Cu)(%)
16.4.2.2措施:
1) 焊条:不要求化学成份与母材完全一致只要机械性能和使用性能不低于母材即可,焊前烘干150-250℃-1-2H,冷裂倾向大时:应选用低氢型焊条。
2) 预热:预热温度在200-300℃之间。
3) 线能量:对于本质细晶粒钢,可采用大的线能量施焊,以降低冷却速度在不预热的情况下减少淬硬倾向和冷裂倾向,对晶粒长大和淬硬倾向大的钢,采用小线能量加预热的方法施焊。在正常焊接速度和预热温度条件下,电流密度应在12.5-17.5A/mm2之间。
4) 焊后热处理:据材料淬硬倾向,结构刚性的大小,工件的厚度,工件结构的复杂程度对工件变形的要求及采用的焊条种类等因素综合考虑,决定是否进行,或进行那种处理。当材料淬硬倾向大,合金成份含量较高,结构复杂,结构刚性大,应进行高温回火处理。当材料淬硬倾向不大,但结构刚性大,焊件热应力较大时应进行去应力退火,当采用酸性焊条可采用碱性焊条但工件或环境潮湿时,应进行焊后消氢处理。高温回火见工程览表,去应力退火500-650℃.消氢处理温度为300-450℃.去应力退火的冷却速度应为≤100℃/H。高温回火的升温率,降温率均应≤200℃/H.高温回火温度应低于或等于原始处理温度。
16.4.3“P”体耐热钢。
16.4.3.1存在的问题:淬硬倾向大,裂纹及脆性破坏倾向大,HAZ软化区的软化,合金元素在焊接时的烧损。
16.4.3.2措施:
1) 焊接材料:化学成份与母材相近并均应略高于母材,高温与常温性能与母材相当,对相当于16Mo,12GrMo,13GrMo44,15CD205,15Mo3材质的材料在拘束度不大时可采用酸性焊条。对于合金含量较高,易淬硬,冷裂的材料10 GrMo910等应采用碱性低氢型焊条。对于可焊性很差,特别是结构刚性大,易裂纹的材料和结构,当对焊缝的强度要求不高时,如Gr5Mo,ZG20GrMoV,Gs17GrMoV511,A40Mo3S,汽缸焊补时,可选用“A”体钢焊条或镍基焊条,以达到不产生组织应力,增加焊缝溶解氢的能力,防止裂纹的目的。焊条在使用前应按规定进行烘干处理。
2) 预热:对于Gr>2.5%的钢,在整个焊接过程中,应始终保持为预热温度值。对于15Mo3、16Mo,及其Gr<2.5%,结构刚性小的材料和结构,在首次预热温度达到后,焊接过程中对温度可不要求始终保持预热温度值。对于需要保持预热温度值的焊缝,预热中断时应先经650-700 ℃的短时回火,以防开裂。预热温度,据Ceg及结构则性情况而公定,可按T=350√eg(1+0.05δ)-0.05(℃)计算。也可按附表16-3工程一览表所给出的预热温度及工艺曲线实施。适应于上式中的Ceg 按Ceg=C+1/9(Mn+Cr)+1/18Ni+7/90Mo计算
3) 提高操作水平,减少焊接缺陷,采用Ar弧焊封底的焊接方法,减少根部缺陷。
4) 改善结构刚性,使焊缝尽可能在自由状态下焊接,妨碍收缩变形的拉筋和系统不必要的拘束应去掉。
5) 必要时,可热状态下对焊缝进行锤击,低于300℃时锤击力量不宜过大,在50℃以下禁止锤击。
6) 焊后缓冷,焊后用保温材料覆盖焊缝接头,最好用硅酸铝纤维材料,覆盖厚度应大于10mm。
7) 焊接参数:采用短段或小线能量施焊,在正常焊接速度下,焊接电流按IH=(30-35)Dh(A)选择,焊条摆动的宽度应小于4倍焊条直径,尽可能采用较小的焊条直径,采用短弧焊接,弧长等于所用焊条直径。
8) 焊后热处理:焊后按规定的规范进行焊后热处理,热处理规范可参照表16-3和工艺过程曲线实施。
16.4.4高Cr热强钢:(如X20CrMoV121)
16.4.1存在的问题:易淬硬冷裂,软化带加宽高温强度下降,合金元素烧损。
16.4.2措施:焊接该类钢,除焊条使用,操作工艺方面的常用措施外还应注意以下几点:
1) 焊条选用:合金成份应近于母材,且略高于母材。尽可能在焊接中避免F出现。
2) 预热:预热大于Ms,但不能大于Ms+50℃,以防F折出,一般在300-450℃之间。
3) 焊接规范:采用小线能量施焊。
4) 焊后冷却:焊后应冷却到100-150℃之间保温0.5-1小时,使M转变完成后再进行回火处理,不得在预热温度直接进行回火加热。不得进行冷焊。
5) 高温回火:回火温度不得大于Acr及原始回火温度,恒温时间,应保证B体完全转变。一般为780-730℃,3.75-8min/mm为宜,恒温时间最少不得低于40分钟。
16.4.5不锈钢
16.4.5.1存在的问题:
1) 合金元素烧损
2) 近缝区脆化。
3) 热裂,柱状晶方向性严重,杂质偏聚。
4) 晶间腐蚀。
16.4.5.2措施:
1) 采用超低碳不锈钢焊条,如A002,A012.
2) 采用有稳定剂的焊条,如A 132,A137对于耐腐蚀性要求低的钢件可采用A 102,A107等,不含稳定剂的焊条。
3) 采用的焊接规范应为小线能量,单层,单道焊。
4) 焊前不预热,焊后快冷。
5) 坡口角度和间隙应尽量小些,不能随意在工件上引弧。
6) 采用钨极氩弧焊工艺。
7) 尽量减小结构中的拉应力。
8) 对接头进行稳定化处理,在800-850℃恒温4小时后空冷。
9) 焊接接头进行固溶处理。在1050-1150℃恒温1小时后空冷。
16.4.6异种钢
16.4.6.1存在的问题
1) 焊缝形成过滤层和焊缝稀释,产生脆性层裂纹。
2) 熔合区产生扩散层,减少接头的寿命。
3) 由于两材料的物理性能的差异,产生较大的附加应力。
4) 焊缝组织不易控制。
16.4.6.2措施:
1) 焊接材料:对于同类组织异种钢,应选择与合金量较低的母材成份相同的焊条或其中间成份的焊条。还可以采用中间成份焊条预过过渡层后,再用与合金含量较低的母材成份相同的焊条焊接。对于非A体易淬硬不同组织异种钢,应采用接近合金含量较低的母材成份或介于中间并含有碳化物形成元素的焊条,对于A体不同组织异种钢(其中之一材料的组织为A,另一材料为非A),必须采用A体钢焊条或采用高Ni焊条预堆,当要求高温强度高时,不得进行预堆。
2) 预热:对于同类组织异种钢,预热温度应接近于合金含量较高的钢的预热温度,非A体不同组织异种钢与同类组织异种钢对预热的要求一致。对于其中之一为A体钢的异种钢,预热温度应等于非A体钢侧材料焊接时的预热温度值。
3) 焊接工艺:采用手工钨极氩弧焊和手工电弧焊,减少熔化比。减小电条或焊丝的直径,厚壁(δ>12mm)结构的材料焊接时,焊条的直径应小于4mm。对δ<12的材料,焊条直径<?3.2mm。采用小的线能量施焊,在正常焊接速度和预热温度条件下,焊接时通过焊条的电流密度应在12-17A/mm2之间,可按H=(30-40)dH选用。采取多层、多道、对称焊的形式,接头的化学元素的成份差较大时,应预堆过渡层。
4) 尽可能提高接头的韧性、对于同一级别的焊条,应选用低氢型焊条,电源极性应为直流反极性连接,当接头的强度要求不高时,可采用低强焊条焊接。
5) 降低接头的附加应力,减小结构拘束度,与工件对口无关的管道固定件应去掉。在加热及冷却时的温度变化率应低于同质接头。
6) 热处理:对于结构刚性大,淬硬倾向大的接头,热处理的起始加热温度应在100~ 150℃之间,对异种钢接头的处理主要是进行高温回火处理,其回火温度,对于同类组织异种负角度非Α同组织异种钢,应接近淬硬倾向大,合金含量高的钢的回火温度。当接头中两种碳化物形成元素浓度差大时,选择两钢回火温度的中间值。
对于其中之一为Α体钢偏向下限的回头温度值。
无论是哪类异种钢接头,其回火温度值均不得高于两中任一钢Αcl。
在钢的加热和冷却过程中,对于含Mo较少的Mn、Si、Cr、镍钢,应避免在250~400℃与500~6
00℃回火脆性区长时间停留,快速通过该区及475℃区。其它区域的加热和冷却应尽量较同质接头慢些。温度变化率为同质接头70-80%。
7) 采用预堆过渡层的焊条的化学成份应为:
(1) 对同类组织和非Α不同组织异种钢应选用充填焊条与高合金侧母材成分之间的焊条。
(2) 对其中之一为Α钢的接头应选用比Α体钢合金含量更高的Α钢焊条或高Ni焊条。
8) 预堆层的厚度应不少4mm。
16.4.7铸铁(灰口铁)
16.4.7.1存在的问题:铸铁的强度低,塑性、韧性差,极易产生白口和裂纹。对冷却速度很敏感。
16.4.7.2措施:
1) 电弧冷焊时
(1) 清理和制作坡口、要求同前
(2) 焊接材料,对于焊接质量要求不高的铸件,可采用Z100焊条;对于受力较大的工件的非机械加工面焊接、可采用Z116、Z117焊条;对焊接质量要求高的重要部件采用Z308、Z408焊条。尽可能选用较小的焊条直径。
(3) 采用小的焊接线能量,在正常焊接速度情况下,焊接电流IH=(28-32)dH选择。
(4) 采用短段、倒退、多层、多道焊接。每段焊道的长度采用Z100、 Z116、Z117时应为10~30mm。采用Z308- Z100408时应为30~50mm。采用直线运条,否则,焊条摆动的幅度应<4dn。
(5) 严格控制焊件的温度,保证在焊下一道焊缝之前,工件焊接部件不大于40℃温差。
(6) 在整个焊接部位,焊道应均匀分布,轮换施焊,降低焊接部件的温度差。
(7) 在热状态对焊缝锤击,锤击的频率较快,随着温度的降低,锤击的力度应逐渐减小。
2) 电弧热焊时:
(1) 清理制做坡口同前。
(2) 必须在水平位置施焊,背面放置衬板及制模.角焊缝庆使焊缝呈船形焊接。
(3) 对钢度较小的构件,应预热到600~650℃,对钢度较大的构件、应预热到650~700℃,
(4) 焊接过程中将部件的非焊接部位进行保温。
(5) 采用较大的焊接线能量施焊,电流密度一般为8~10A/mm?;
(6) (采用铸铁芯焊条?8-?14毫米。)
(7) 预热时的升温率<200℃/H,且加热均匀。
(8) 焊接要一次完成。
(9) 焊后工作应在保温的条件下缓冷,降温率应<100℃/H
3) 气焊时:
(1) 清理制做坡口同前。
(2) 必须在平焊位置施焊及制模;对角焊缝应放在船形位置焊接。
(3) 采用铸铁芯焊条。
(4) 火焰应为中性焰。
(5) 采用碱性剂,气剂201。
(6) 尽量使焊缝整个表面保持较高的温度。
(7) 火焰及铸铁焊芯的搅拌应保证母材有足够的熔深。
(8) 焊接应一次完成。
(9) 焊后工件应保温缓冷。降温率<100℃/H
16.4.8铝和铝合金
16.4.8.1存在的问题:
1) 导热性强,热容量大,散热损失大,易出现未焊透。
2) 线胀系数大,易产生严重的变形。
3) 熔池易滴落,焊缝成形差。
4) 形成难溶杂质,易造成焊缝夹杂物。
5) 易形成H气孔。
6) 熔化时难判断、操作困难。
7) 熔点及高温强度低,时效的高强合金有较大的结晶裂纹倾向,在焊缝及半熔化氏易产生低塑性裂纹。
16.4.8.2措施:
1) 选用热量集中的热源,对于大厚工件采用交流氩弧焊,电弧焊。对小而薄的工件可采用气焊。
2) 选用适当的坡口尺寸。据工件厚度的不同选择不同的坡口型式。δ=3-4毫米时不开坡口,δ<3毫米时采用卷边焊,δ=4-12毫米时采用“V”60-90°坡口,δ>12毫米采用 “X”80°坡口 。
3) 焊前装配夹具垫板或制模,水平焊接。
4) 工件及焊丝的清理同前,焊条按规定进行烘干。一般为150-1-2H0 。
5) 焊前进行200-400℃预热。对于薄板及小件采用Ar弧焊时预热温度可选较低值。
6) 正确选择焊接材料中,据不同的焊接按表16.6选择。
7) 正确选用焊接参数,电弧焊按表16.7选择,手工氩弧焊按表16.8选择。
8) 气焊时,采用中必焰,左向焊法,搭接接头应放在船形位置。
9) 对气焊及电焊后的焊渣应进行严格的清理。电弧焊时,应采用直流反极性连接。
表16.6 不 同 工 件 材 料 材 质,不 同 焊 接 方 法的 焊 接 材 料 表
工件材料 交流TiG焊 电弧焊 气 焊
材 质 焊 丝 焊 条 焊 丝 焊 粉
AI及性能要求
不高的AI合金 丝301
丝302 L109 丝301
丝302 气剂401
AI-Si合金 丝311 L209 丝311 气剂401
AI-Mn合金 丝321 L309 丝321 气剂401
AI-Mg合金 丝331 L309 丝331 气剂401
表16.7 AI及AI合金手工电弧焊规范参数表
工 件
厚 度 坡 口
型 式 对 口
间 隙
mm 层 数 道 数 焊 条
直 径
mm 焊 接
电 流
A 总层数 总道数
第几层 几层道数
<3 卷 边 0 1 1 3.2 80-110 1 1
3-4 不开坡口 2 1 1 3.2 80-110 2 2
2背 1背 3.2 80-110
4-6 V 2 1-3 1 3.2 80-110 3 3
6-9 V 2.5 1-2 1 3.2 80-110 3 3
3 1 4 110-150
9-14 X 2.5 1-2
3-4 1 3.2
4 80-110
110-150 4 4
15-20 X 2.5 1-2 1 3.2 80-110 4-5 6-7
3-4 1 4 110-150
4-5 2 4 110-150
表16.8 手工TiG焊参数表:(平焊)
工 件
厚 度
mm 坡 口
型 式 焊 层
数 焊 接
流IHA 焊接速度
wHmm/
min 钨 极
直 径
mm 焊 丝
直 径
mm 氩 气
流 量
mm 喷 嘴
直 径
mm
1-1.2 I 1 65-80 300-450 1.6/2.4 1.6/2.4 5-8 8-9.5
2 I 1 110-140 280-380 2.4 2.4 5-7 8-9.5
3 I 1 150-180 280-380 2.4/3.2 3.2 7-10 9.5-11
4 V 1-2背 180-210 200-300 3.2/4.0 3.2/4.0 7-11 11-13
6 V 1-2 230-270 200-300 4.0/5.0 4.0/5.0 8-11 13-16
9 V 1-2 280-340 120-180 5.0 5.0 10-15 16
12 V 1-3 350-400 150-200 6.4 6 10-15 16
12 X 1-4背 340-380 150-250 6.4 5 10-15 16
注:弧长为1.5-4.0毫米,极钨极伸长喷嘴长度为5-12毫米。其它位置时,IH应减小5-10%,WH应小20-30%。
10) 焊接应一次完成。
11) 其它要求见手工钨极氩弧焊工艺。
16.4.9铜及铜合金。
16.4.9.1存在的问题:
1) 导热性高,操作困难。
2) 熔合线近区晶粒易长大。
3) 产生脆性共晶和杂质聚集。
4) 近缝区产生气孔和裂纹。
5) 合金元素烧损。
16.4.9.2措施
1) 对于大而厚的工件采用能量集中的热源,如电弧焊,氩弧焊。对于小而薄的工件可采用气焊。
2) 采用正确的坡口型式和尺寸,δ<4毫米的工件可不开坡口对接或卷边焊;δ=4~10毫米的工件采用“V”型坡口,坡口角度为60-70之间,钝边厚度为0~1mm。间隙2~4mm。δ>10 mm采用“X”坡口。
3) δ>4mm的工件,应进行250~400℃的预热。铜合金选择较高的预热温度值,铜采用较低的预热温度值。
4) 焊接极性的选择,电弧焊采用反极性连接,ΤiG焊采用正极性连接。
5) 焊丝的坡口清理,焊条的烘干要求同前面所述。
6) 焊件的厚度较大时,可采用垂直或半垂直焊。(ΤiG焊)
7) 焊缝后面应置垫板或制模,对于不要求焊缝透度可不采取此措施。
8) 正确地选择焊接材料,对于不同工件材质,不同焊接方法按表16.9进行选择
表16.9 不同工件材质、不同焊接方法的焊接材料表
工 件 材 质 电 弧 焊 氩 弧 焊 气 焊
焊 条 焊 丝 焊 丝 焊 粉
导电钝铜 T107 丝201 丝201 粉301
铜 T107、T227 丝201-丝202 Qsi31、 QSn4-0.4 粉301
黄铜 T227 、T237 丝221-丝224 Qsi3-1 粉301
锡青铜 T237 QSn4-0.4 QSn4-0.4 粉301
Qsi T237 Qsi3-1 Qsi3-1 专用焊粉
QAI T237 QAi4 QAi4 粉401
注:粉X X X =气剂X X X
QSi接专用焊纷配方:%
配方1 配方2:
药 品 硼 砂 氟化钠 药 品 硼 砂 无水磷酸钠 氯化钠
成 分 90 10
成 分 72 15 13
9) 正确地选用焊接参数,据不焊接方法按表16.10、表16.11选择。
表16.10 铜 合 金 手 工 电 弧 焊 参 数 表
工 件
厚 度
mm 坡 口
型 式 对 口
间 隙
mm 层 数 道 数 焊 条
直 径
mm 焊 接
电 流
A
第n层 总层数 层道数 总道数
<3 卷边 0 1 1 1 1 3.2 90-130
3-4 I 0-1 1 2 1 2 3.2 90-130
2背 1背 3.2 90-130
4-6 V 2-4 1-3 3 1 3 3.2 90-130
6-9 V 2-4 1-2 3 1 3 3.2 90-130
3 1 4.0 110-160
9-14 X 2-4 1-2 4 1 4 3.2 90-130
3-4 1 110-160
15-20 X 2-4 1-2 4-5 1 6-8 3.2 90-130
3-4 2 3.2 90-130
4-5 2 4.0 110-160
注:纯铜焊接时焊接电流相应增加10-20%。
10) 焊件应使焊缝处平焊位置,采用短弧,直线运弧。
表16.11 TiG 焊 工 工 艺 参 数 (Cu及青铜氩弧焊)
工 件
厚 度
mm 坡 口
型 式 焊 层
数
第几层 焊 接
流IHA 焊接速度
wHmm 钨 极
直 径
mm 焊 丝
直 径
mm 氩 气
流 量
V/min 喷 嘴
直 径
mm
1 I 1 100-120 250-350 2.4 1.6 5-8 8-10
2 I 1 150-180 250-300 3.2 2.4 5-8 8-10
3 I 1-2背 190-210 200-280 4.0 3.2 7-10 9-11
4 V 1-2背 210-250 130-250 4.0 3.2/4.0 8-11 11-13
6 V 1-2 270-310 130-250 5.0 4.0/5.0 8-11 13-16
9 V 1-2 320-380 90-150 6.0 5 10-15 16
10-12 X 1-4背 400-440 110-160 6.0 5 10-15 16
11) 采用Ar弧焊丝应置于电弧与母材之间。
12) 黄铜采用TiG焊时,应比表16-4-6的电流值小20%。
13) 纯铜和铜合金结构刚性较大时,可用平头锤快速击锤焊缝消除应力,但锡青铜不得锤击和冲击。
14) 气焊时铜及青铜要采用严格的中性焰,黄铜应用轻微的氧化焰。
16.5 焊后热处理工艺
16.5.1需要焊后热处理的焊接接头:
1) δ>30mm的低碳钢管件。
2) δ>32mm的低碳钢压力容器及结构。
3) δ>28mm的普低钢压力容器及结构。
4) 耐热钢管件及结构。
5) 堆焊焊条的堆焊结构。
6) 强腐蚀介质中的受载不锈钢结构及黄铜结构件。
7) 含H量较高的焊缝结构。
16.5.2在焊前预热、焊后保温缓冷及结构应力较小的条件,可不进行热处理的焊接接头
1) δ≤10mm的15M03、13CrM044 、15 Cr M0管、板结构。
2) δ≤6mmd≤89mm的10 Cr M09 910管件及结构。
3) 冷却水A体不锈钢管道不进行焊后高温回火处理。
16.5.3对不同的材料及结构采取不同的热处理方法。
1) 对于低碳钢及低碳低合金钢刚性结构,在强腐蚀介质中存在拉应力作用的不锈钢结构,在氯化物的介质中使用的黄铜构件,焊后均应进行去应力处理。
2) 对于已出现б相的A体不锈钢接头应进行固溶处理。
3) 对于有析出б相倾向的A体不锈钢,焊扣应进行稳定化处理。
4) 对于淬硬倾向较大的合金钢及堆焊材料,焊后应进行高温回火处理。
16.5.4热处理热源的选择,本着使接头各点间由于热处理加热形成的温差应力与其它应力总种小于材料的强度极限的原则及所需热源功率的大小进行选择。
1) 对于淬硬倾向小,结构刚性较大的钢结构进行消氢处理和去应力处理,可以采用火焰加热。
2) 对于淬硬倾向较大的钢种,结构应力较小时 ,可采用电阻炉,远红外线炉加热。
3) 对于淬硬倾向很大或淬硬倾向较大,结构应力也较大的钢种及结构采用感应加热。各种钢结构采用的热处理热源如表16.12.
16.5.5热处理规范参数选择:
1) 热处理温度见工程一览表附表16-3及堆焊材料的热处理温度表附表16-4,异种钢接头的加热温度应低于低合金侧母材的Acl,并尽可能靠近高合金侧母材的热处理温度的要求值。
2) 恒温时间应不同材料的不同厚度进行选择,常见材料热处理恒温时间见附表16-3.附表16-4,及附图16-3.
3) 升温率和降温率的选择,升温率应使焊接接头内外任意两点间的温差≤50℃,对于堆焊的硬质合金其温差≤40℃,降温率应使焊接接头中的残余应力在允许的范围内。升温率和降温率可依据附表16-3及附图16-3进行施实,在一览表及工艺曲线上查不到的,按250×250/δ℃/计算,且不大于300℃/Η,对于结构用钢温度降至300℃以下时,可使其在保温材料中自然冷却,不再进行控温操作。
16.5.6加热宽度
对于对接焊缝、角接焊缝,应自焊缝中心起母材两侧≮3в,且≮30mm,(B为焊缝宽度,)对于堆焊层,应比堆焊部位增加25-30 mm,或进行整体加热。
发热元件的宽度应比加热每侧增宽20~30mm。当工件厚度δ<25mm时,采用较小值,当δ>25mm时采用较大值 。
表16.12 各种热源所适应的材料及厚度
材 料 类 别 不同热源火焰适应的工件厚度 单位:mm
火 焰 电阻、红外线炉 电感应炉
低碳钢、普低钢 δ<20 δ=20-35 δ>35
中碳钢、中低合金钢 δ<12 δ=12-20 δ>20
高合金结构 δ≤10 δ>10
堆焊焊层 各种厚度
16.5.7保温层的宽及厚度:其宽度应比发热元件每侧增宽120~240mm,且增宽值>保温层厚度。厚度与预热要求相同。
16.5.8保温材料:采用硅酸侣保温材料。
16.5.9对热源功率的要求:应使热源输出功率大于头加热所需功率。材料加热需要的功率可由以下两式概算:
1) Q=K.W.C(T-To)
P=Q/0.24t
式中:P—加热所需功率,单位:KW
Q—被加段加热到T时所需热量。
单位:KcaL。
K—热损失系数,一般为2.5~3.5.
W—被加热段重量、单位:kg
C—比热、单位:KcaL/kg℃
T—热处理温度、单位:℃
To—初始温度、单位:℃
t—加热所需时间。单位:S
2) P=AD√S---
A=K.(T/620)?
式中:P—加热所需功率、单位:KW
D—管径、单位:m
S—工件厚度。单位:mm。
T—加热温度。单位℃
Κ—绝热消耗系数。内外绝热时,Κ=5,外绝热时Κ=10,无绝热时Κ=15.
16.5.10感应加热参数计算:
1) 加热器内径:Dc=D+2δ
式中:D=管径。mm
δ—绝热层厚度mm
2) 加热线圈匝数及其截面积计算:
被加热段电阻:R=PL1S0(Ω).
被加热段电流:I=√P/R-------(A)
被加热段感应电势:E=P/I0COS?(V)
式中:ρ—电阻率(Ωcm2/cm)
L—管长度(cm)
S0—有交通电截面,工频S0=0.2 B。
B—加热宽度(cm)
P—需加热段功率(W)
COSф---功率COSф=0.6
感应线圈匝数:N=U/E(匝)
感应线圈电流:I=E/U.Io(A)
感应线圈堆面积:S=I/I(mm)2
式中:U—感应线圈两端电压/(V)
i—许用电流密度、(A/mm?),铜为i=2.5A/ mm?,铝为i=1.5A/ mm?
16.5.11电阻加热:据加热所需的功率,外形尺寸按附表16-6选用。
16.5.12测温及控温
1) 测温,对于电阻冖,红外线炉,感应加热 ,应采用固定热电偶测温。对于火焰加热,采用点温计间断测温。
2) 测温点的设置,对于δ>25工件自焊缝到边缘至少有两个测温点。对热处理条件要求严格的材料,应另外装设不少于两个的备用测温元件。测温原件应分别布置在下部、上部、焊缝及要求加热宽度的边缘。
3) 控温、对于采用电阻炉,红外线炉,感应加热的主蒸汽、再热蒸汽,给水管道及其它硬淬倾向大的中、高合金钢工件应采用自动控温装置控温及记录。对于其它热处理要求不十分严格的薄壁中、低合金及低碳钢工件可以采用人工控温方式进行控温和记录。
4) 热处理用的全部仪器、仪表、设备及其附件在使用前进行检查和校验。
16.5.13热处理结束后:在所处理的接头上打上热处理工的代号钢印。整理好记录交给班组存档。
16.5.14热处理中注意的几个问题:
1) 当工件厚度>50mm时,易裂纹的材料应进行中间去应力处理。每25mm进行一次,温度为520-560℃、恒温0.5H,其它参数同前。
2) 避免加热温度达到Acl,对于有较大软化倾向的钢禁止超过原始处理温度
3) 对于含有强碳化物形成元素如V、C、Mo、Ti、Nb的钢,应避开(避免长时间停留)600℃左右的再热裂纹敏感区。
4) 对于F体耐热钢,应避开475℃及650-850℃脆化区。
5) “A”体耐热钢应避开500-875℃脆化区。
6) 补偿导线必须与热电偶相匹配。
7) 测温仪表必须与测温元件相匹配。
16.6 焊接及热处质量检查和质量标准`
16.6.1质量检查
1) 所有的焊接过程中,均应对其各层道的表面进行焊工自检,对于重要的接头应做氩弧打底层的检查或中间检查,出现问题应处理完善后方可进行下道工序。
2) 必要时应根据实际情况,进行代样断面、机械性能及金相方面的检查。
3) 焊接接头的检查方法,范围及数量见表16.13.
表16.13 焊接接头的检查方法、范围及数量
检查方法 范 围 数 量 备 注
外 观 全部焊接接头 100%
热处理后硬度 D<194及δ<12(mm) 5%
代 样 D≥194及δ>12 100%
无损探伤 主蒸汽、再热蒸汽、给水管道及等参数管道工作温度>450℃,直径>159mm的蒸汽管道、除氧器 100% 质量可靠性低时按水电部(金属焊缝射线篇)I级标准
主蒸汽,再热汽管道的疏水管道的低压侧。高压加热器疏水管道。给水管道的放水和高压侧。工作压力>100kg/cm2及工作温度>450℃、直径≤159mm的管件。工作温度=300~450℃,直径>159mm的蒸汽管道。工作压力>60kg/cm2热水管道。P>25kg/ cm2 油管道 25%
P<16 kg/ cm2 低压溶器、直径>76mm的汽、水、油管道 25% Ⅱ级
4) 当δ<21mm的管子只作超声波检查时,还应作≮20%的射线检查。
5) 合金钢焊缝经热处理后应进行硬度检查。
6) 外观焊缝不合格时,不能进行其它项目的检查。
7) 对于检查不合格的项目做双倍复检,复查仍有不合格者,该批接头为不合格。
8) 工程中不合格焊缝应进行返修。
9) 热处理不合格焊缝应重新处理。
16.6.2质量标准
16.6.2.1外观质量标准:
1) 焊缝边缘应园滑过渡到母材,外形尺寸允许值见表16.14
2) 焊缝表面缺陷合格范围见表16.15.
3) 焊缝角变形允许范围见表16-16.
表16.14 焊缝外形尺寸允许值 单位:mm
焊 缝
型 式 加强面高度 加强面高低差 焊缝宽度 焊 脚
平 焊 其 它 平 焊 其 它 比坡口单侧增宽 尺寸差
≯3 ≯4 ≯2 ≯3 1-2
≯2 ≯3 0-3
表16.15 焊缝外表缺陷允许范围
缺陷名称 允 许 范 围
裂纹、未熔合、表面气孔和夹渣 不允许
咬边 深度:≤0.5mm
总长度:板件≤焊缝总长10%,管件≤焊缝总长的10%,且≤40mm
内凹、未焊透(代样) 深度:≤0.1倍壁厚
总长度:≤焊缝总长10% 氩弧焊打底不允许未焊透
焊瘤(管件代样)板件 板件及直径<108mm管件,其高度≤3mm,直径<108mm管件,满足通球检验标准
表16.16 焊 接 角 变 形 允 许 范 围
焊件类别 偏差值 示意图
mm 0 αmm mm
板件 ≯3° ---
管件 直径<100 --- ≯1
直径≥100 --- ≯2
16.6.2.2焊接接头机械性能应符合表16.17标准
表16.17 焊 接 接 头 机 械 性 能 标 准
试验项目 合 格 标 准
抗拉强度 不低于母材规定值下限
冷 弯 碳素钢90°d=2δ
合金钢50°d=3δ D弯轴直径
δ:试样厚度
冲击韧性
kg.m/cm2 碳素钢≥6
合金钢≥5
热处理后硬度
HB ≤母材硬度+100、、且≤350
注:(1)堆焊材料的硬度要求除外。
(2) 弯到规定角度后,拉伸部位上的横向裂纹≯1mm,纵向裂纹≯3mm
(3)焊缝断口不允许有超过折断面检查允许范围的缺陷。
(4)需做热处理的焊缝应先做热处理。
表16.18 折 断 面 和 金 相 宏 观 检 查 标 准 单位:mm
缺 陷 种 类 厚 度
≤6 >6
内凹 深度≯25%δ,且≯1 深度≯20%δ,且≯2
单个气孔 径向≯25%δ或1.5
轴向,周向≯2 径向≯25%δ或4
轴向,周向≯30%或≯2
壁厚方向同一直线上各种缺陷总和 ≯25%δ且≯1.5
≯25%δ、且≯4
裂纹、未溶合 不允许
根部未焊缝 总长度≯10%周长,深度≯15%δ,且≯1.5
沿壁厚度方向同一直线上各种缺陷的总和 每1cm2 ≤0.8直径气孔或夹渣不超过5个或总面积不超过3mm2。沿园周(或长度)方向10倍壁厚的范围内,气孔和夹渣的累计长度不超过壁厚(相邻缺陷间距离超过最大缺陷长度的5倍时,则按单个论)
16.6.2.3焊接接头折断面和金相微观标准应符合表16.18规定。
16.6.2.4金相微观标准:
1) 无裂纹
2) 无过烧组织。
3) 在非马氏体钢中,无马氏体组织。
16.6.2.5焊缝射线检验评级标准:
1) 有裂纹或未溶合的焊缝为IV级。
2) 气孔(包括点状夹渣)的评级标准
(1) 也按评片标准尺上的10×20计数范围框进行点状缺陷计数。
(2) 单个气孔(包括点状夹渣)最大直径不得超过壁厚的三分之一。
(3) 点状缺陷评级标准见表16.19
表16.19 点 状 缺 陷 评 级 标 准
级 别 不同壁厚时的缺陷点数
壁 厚 mm
2~6 >6~10 >10~20 >20~50 >50~120
Ⅰ 1 2 3 4 6-10
Ⅱ 3 5 7 10 12-18
Ⅲ 5 7 10 14 20-26
Ⅳ >Ⅲ标准者
(4) 不同尺寸的气孔或点关夹渣按表16.20的系数进行折合。
表16.20 点 状 缺 陷 计 数 换 算 系 数
直径(mm) ≥0.5 >0.5-1 >1-1.5 >1.502 >2-3 >3-4 >4-6 >6-8
点系数 0.5 1 2 3 4 7 12 20
(5) 对于小径管,沿焊缝厚度方向有针状孔时评为不合格。
3) 条状夹渣群的评级标准见表16.21,当焊缝长度<12δ(Ⅱ)或6δ(Ⅲ)时、条状夹渣群总长可按比例折算,如持算的夹渣长度小于单个条状夹渣长度时,按单个条状夹渣允许值评级。当夹渣长度比>3或长度≥4mm时,视为条状夹渣。
表16.21 条 状 夹 渣 群 评 级 标 准
级 别 单 个 长 度(
mm) 夹 渣 间 距
(mm) 条状夹渣群总长度
(mm)
Ⅰ 0 0 0
Ⅱ 1/3T最小为4
最大≯20 <6L
≥6L 不超过单个夹渣长度在任何12δ焊缝长度内≯δ
Ⅲ 2/3 T最小为6
最大≯30 <3L
≥3L 单个夹渣长,在任何6δ焊缝长度内δ
Ⅳ 大于Ⅲ级标准者
注:L---两相邻夹渣中较大者尺寸,δ---壁厚。
4) 根部未焊透评级标准:
(1) 对d≤76mm管的未焊透按表16-6-10规定评级。
表16.22 d≤76mm管根部未焊透评级标准
级 别 未焊透深度占壁厚的百分比(%) 连续或断续未焊透总长占焊缝周长的
百分比(%)
Ⅰ 0 0
Ⅱ ≤10 ≤10
Ⅲ ≤15 ≤10
Ⅳ 大于Ⅲ级标准者
(2) d>76mm管焊缝根部未焊透按表16.23的规定评定。
5) 焊缝质量的综合评级:
(1) 在12δ焊缝长度内几种缺陷同时存在时,应先按各类缺陷分别评级,最后综合评级。
(2) 如有两种缺陷,应将其级别数之和减1作为缺陷综合的焊缝质量等级,如有三种缺陷,应将其级别之和减2作为缺陷综合的焊缝质量等级,依次类推。
(3) 管道、联箱等环形焊缝,应以整个焊缝的周长进行质量评判。分段透照的焊缝应将底片搭接部位搭接起来进行评判。
表16.23 d>76mm根部未焊透评级标准
质 量
等 级 未 焊 透 深 度
连续或断续未焊透总长
(mm)
占壁厚百分比
(%)≯ 极限深度
(mm)≯
Ⅰ 0 0 0
Ⅱ 10 1.5 间距<6L时,不超过单段未焊透长间距≥6L时,在任何12δ焊缝长度内≯δ
Ⅲ 15 2.0 间距<3L时,不超过单段未焊透长
间距≥3L时,在任何6δ焊缝长度内≯δ
Ⅳ 大于Ⅲ级标准者
注:L---未焊透长度,δ---壁厚
表16.24 d≤76mm管根部内凹评级标准
级 别 内 凹 深 度 内凹总长占焊缝周长的百分比(%)
占壁厚百分比(%)极限深度mm
Ⅰ ≯10 ≯1 ≯30
Ⅱ ≯15 ≯2 ≯30
Ⅲ ≯20 ≯3 ≯30
Ⅳ 大于Ⅲ级标准者
注:内凹总长为连续或断续内凹的总和。
表16.25 d>76mm管根部内凹评级标准
级 别 内凹占壁厚百分比(%) 内凹总长占焊缝总长的百分比(%)
Ⅰ ≯10 ≯
Ⅱ ≯15 ≯25
Ⅲ ≯20 ≯25
Ⅳ 大于Ⅲ级标准者
16.6.2.6焊接试样取样及规格。
1) 取样:
(1) 用机械方法取样,否则应将气割等切口的HAZ区去掉5mm以上。
(2) 板件试样切取部位见图16.2.
1— 面弯试样
2—断口试样
图16.2
(3) 水平固定管焊缝的切取位置见图16.3.垂直固定管焊缝不作规定。
1.2—拉力试样。
3、6、9—折断面试样
4、5--弯曲(面弯、背弯)试样
7、8—金相试样
图16.3
2) 试样规格:
(1) 拉力试样规格如16.4及表16-6-14
L1—按试验机确定。
图16.4
表16-6-14 拉 力 试 样 规 格 尺 寸 (mm)
试样厚度δ B L L1
≤4.5 15±0.5 50+2 L1 按 试 验 机
确 定
>4.5~10 20±0.5 60+2 L1
(2) 冷弯试样规格如图16.5.
δ—试样厚度
D—弯曲直焊
β=1.5δ
L= D+2.5δ+80
图16.5
(3) 金相试样规格如图16.6.
δ—壁厚
B—10—20mm
L—试样长度,包括焊缝及基本金属
图16.6
(4) 断口检查试样规格见图16.7
δ1=1/4δ
B=2δ且≮10mm
图16.7
(5) 冲击试验试样规格见图16?.8
文章末尾固定信息
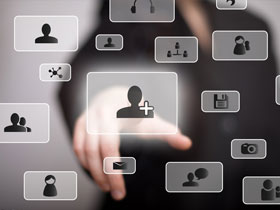
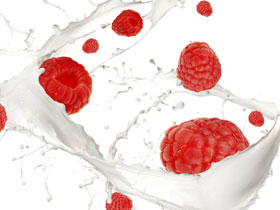